How Coatings and Finishes Enhance Bolt Durability
- emergemarketingind
- Feb 20
- 1 min read
Bolts are essential in construction, manufacturing, and industrial applications. However, their durability depends on protective coatings and finishes. Without proper coatings, bolts can corrode, weaken, and fail under stress. This is why foundation J bolts, foundation bolts, and stud bolts require high-quality coatings to ensure long-term performance.
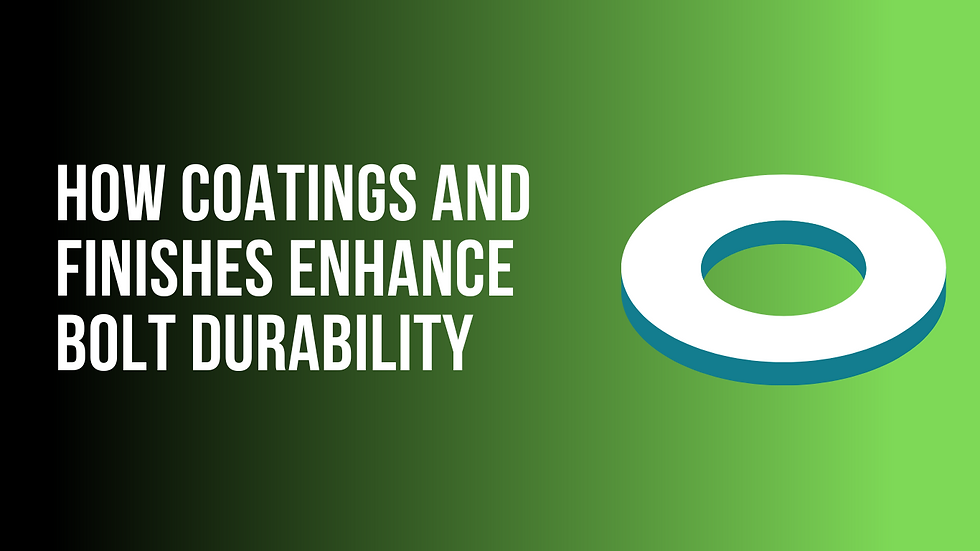
Why Are Coatings Important?
Coatings act as a shield against corrosion, wear, and environmental exposure. Anchor bolt manufacturers and U bolts manufacturers use advanced coating techniques to enhance bolt strength and efficiency. Uncoated bolts can rust, reducing their reliability and lifespan.
Types of Coatings for Bolts
Different coatings serve specific purposes based on industry needs:
Zinc Coatings – Common in foundation bolts, these provide excellent rust resistance.
Hot-Dip Galvanized – Ideal for foundation J bolts used in outdoor and marine applications.
PTFE (Teflon) Coatings – Reduce friction, improving efficiency for stud bolts in industrial settings.
Epoxy Coatings – Highly durable and resistant to weathering, commonly used by stainless steel U bolt manufacturers.
Benefits of Coated Bolts
Industries using coated bolts experience multiple advantages:
Extended Lifespan – Protective layers enhance durability, crucial for anchor bolt manufacturers.
Lower Maintenance Costs – Coated bolts require fewer replacements, saving money.
Improved Strength & Performance – Coatings help bolts withstand high stress, benefiting U clamp manufacturers.
By investing in high-quality coatings, U bolts manufacturers and other industries can ensure superior bolt performance, reducing long-term maintenance costs and increasing efficiency. Choose the right coating to enhance bolt longevity and reliability.
Comments