How Washers Prevent Galling and Seizing: A Crucial Guide
- emergemarketingind
- Feb 13
- 2 min read
When metal fasteners come into contact under high pressure, they can stick together due to friction and heat, leading to galling and seizing. This issue is especially common in applications involving stainless steel bolts, nuts, and industrial washers. Galling occurs when microscopic welds form between the surfaces of fasteners, making them difficult to remove or adjust. If not addressed, it can lead to permanent damage, costly repairs, and compromised fastening reliability.
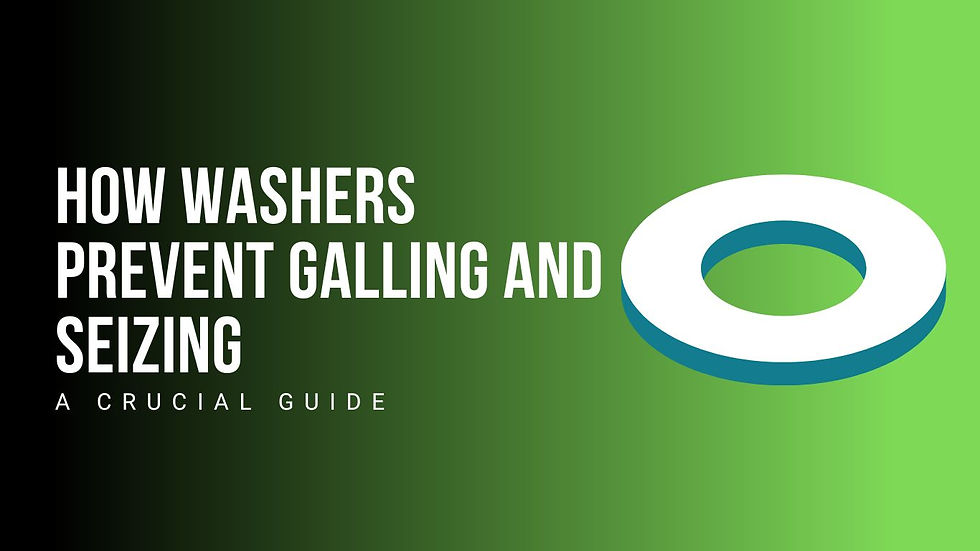
Using the right washer between metal fasteners acts as a protective barrier, reducing friction and preventing galling. Different types of washers help in different ways. Shim washers, for example, are precision-thin washers designed to create the right spacing and minimize friction. Leading shim washer manufacturers offer them in various materials to suit industrial needs. Spring lock washers provide tension to hold fasteners securely, while external tooth lock washers have serrated edges that grip surfaces and prevent rotation. Similarly, hex washers offer enhanced stability for heavy-duty applications, and self-locking washers lock the fastener in place, reducing the risk of seizing.
Different washer manufacturers offer a variety of machined washers to tackle galling and seizing effectively. Fender washers, with their large diameter, distribute load evenly and reduce material stress. Wedge lock washers are specifically designed for high-vibration environments to ensure fasteners remain secure. Sealing washers, which feature rubber or silicone layers, not only prevent leaks but also protect against corrosion. In construction, ogee washers—which are thick and curved—provide extra support, while tab washers have small tabs that lock them in place to prevent rotation.
Conical washers are known for their ability to provide spring-like tension for heavy-load applications. Meanwhile, square washers offer better load distribution compared to traditional round washers, and countersunk washers are ideal for applications that require a flush fit for a smooth finish.
To maximize the effectiveness of washers, it is essential to follow best practices. First, selecting the correct industrial washer for the application is crucial. Using coated or lubricated washers, such as zinc-coated or PTFE-coated options, helps reduce friction and wear. Proper installation is also key—placing the washer correctly between the fastener and surface ensures maximum performance. Regular inspection and replacement of worn-out washers further enhance fastening efficiency and longevity.
Preventing galling and seizing is essential for maintaining strong and long-lasting fasteners. By incorporating high-quality washers—such as shim washers, wedge lock washers, sealing washers, and conical washers—fastening systems can operate smoothly, reducing wear and extending component lifespan. For those seeking reliable fastening solutions, choosing precision-made machined washers from trusted washer manufacturers ensures durability and optimal performance in industrial applications.
Comments