The Role of Specialty Washers in Unique Applications
- emergemarketingind
- Jan 30
- 3 min read
Specialty washers play a unique role in various applications that require specific features. From ogee washers to conical washers, these components are designed for highly specialized uses. Understanding the materials and manufacturing processes behind these washers will help you choose the best option for your specific needs. Whether you are sourcing shim washers from shim washer manufacturers or looking for machined washers, understanding the right material and manufacturing process is key to ensuring optimal performance.
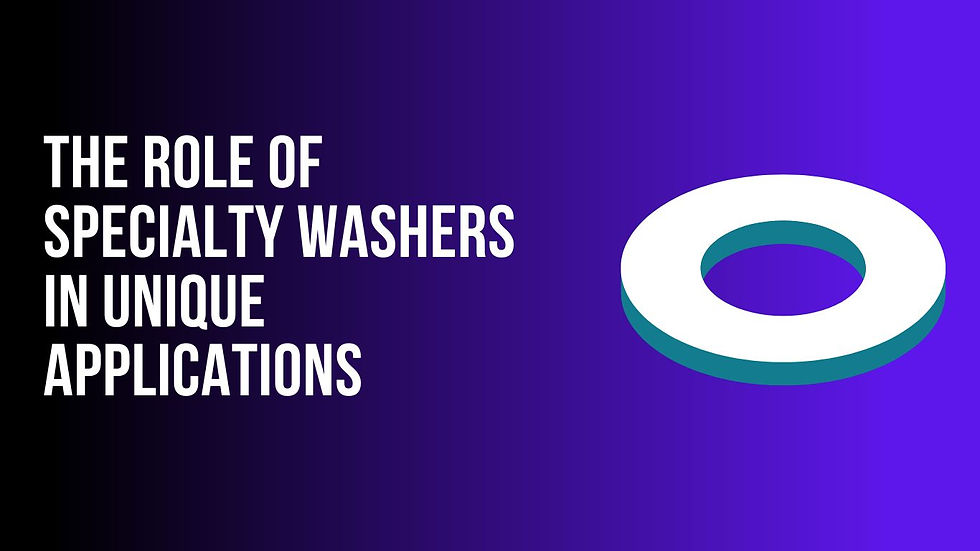
Types of Specialty Washers
Ogee Washers: These washers are commonly used in electrical assemblies, where high conductivity is required. Ogee washers are often sourced from washer manufacturers who specialize in high-conductivity materials like brass or stainless steel.
Tab Washers: Ideal for preventing loosening in automotive or industrial applications. Tab washers are designed to lock into place and prevent the fastener from backing out due to vibrations or other forces. They are commonly used in both industrial washer and machined washer applications, ensuring the fastener stays securely in place.
Conical Washers: These washers provide a spring-like effect and are often used in suspension systems, machinery, and other applications that require tension or load distribution. Conical washers are particularly effective when sourced from shim washer manufacturers who provide washers that can handle extreme pressure without deforming.
Sealing Washers: Used to prevent leakage in sealing applications, these washers are designed with a rubber or plastic insert to create a tight seal. Sealing washers are often found in industries such as plumbing and automotive, where leak prevention is critical.
Wedge Lock Washers: These washers lock into place to prevent loosening of fasteners. Wedge lock washers are commonly used in heavy machinery, automotive, and construction applications.
Square Washers: These washers are designed to distribute loads evenly over a large area. Square washers are often used in applications where there is a need to reduce surface damage.
Materials Used in Specialty Washers
Stainless Steel: Offers corrosion resistance, making it ideal for outdoor and marine environments. Stainless steel is commonly used in ogee washers, tab washers, and fender washers to ensure durability in harsh environments.
Brass: Provides excellent electrical conductivity and is used in applications requiring conductive properties. This material is often chosen for ogee washers and sealing washers in electrical or water-tight systems.
Carbon Steel: Known for its strength and cost-effectiveness, carbon steel is used for industrial washers, external tooth lock washers, and spring lock washers.
Titanium: Used for high-performance applications, titanium washers are often chosen for aerospace and medical devices. Machined washers made from titanium are precision-engineered to meet the strictest tolerance requirements.
Aluminum: Lightweight and corrosion-resistant, aluminum washers are commonly used in aerospace and automotive industries.
Manufacturing Process for Specialty Washers
Stamping: The stamping process is often used by washer manufacturers to produce large quantities of shim washers, square washers, and spring lock washers. The process involves cutting washers from flat sheets of metal using a stamping die.
Machining: For high-precision washers, machining is the preferred method. Machined washers are made using CNC equipment to meet the strictest tolerances. This process is commonly used for countersunk washers, self-locking washers, and conical washers that require exact dimensions.
Heat Treatment: Some washers, such as wedge lock washers and external tooth lock washers, undergo heat treatment to improve their strength and resistance to wear and tear. This process involves heating the washer to a specific temperature and then cooling it rapidly.
Coating: To further enhance corrosion resistance, fender washers and sealing washers often undergo coating processes such as zinc plating or anodizing.
Conclusion
Whether you’re using ogee washers, tab washers, or conical washers, selecting the correct material and manufacturing process is crucial to the performance and longevity of your application. Always source your washers from reputable washer manufacturers who understand the nuances of each washer type, including shim washers, machined washers, spring lock washers, and others. By doing so, you can ensure that your washers deliver the required performance and durability for your specific needs.
Comments